Can You Use Transfer Tape to Laminate?
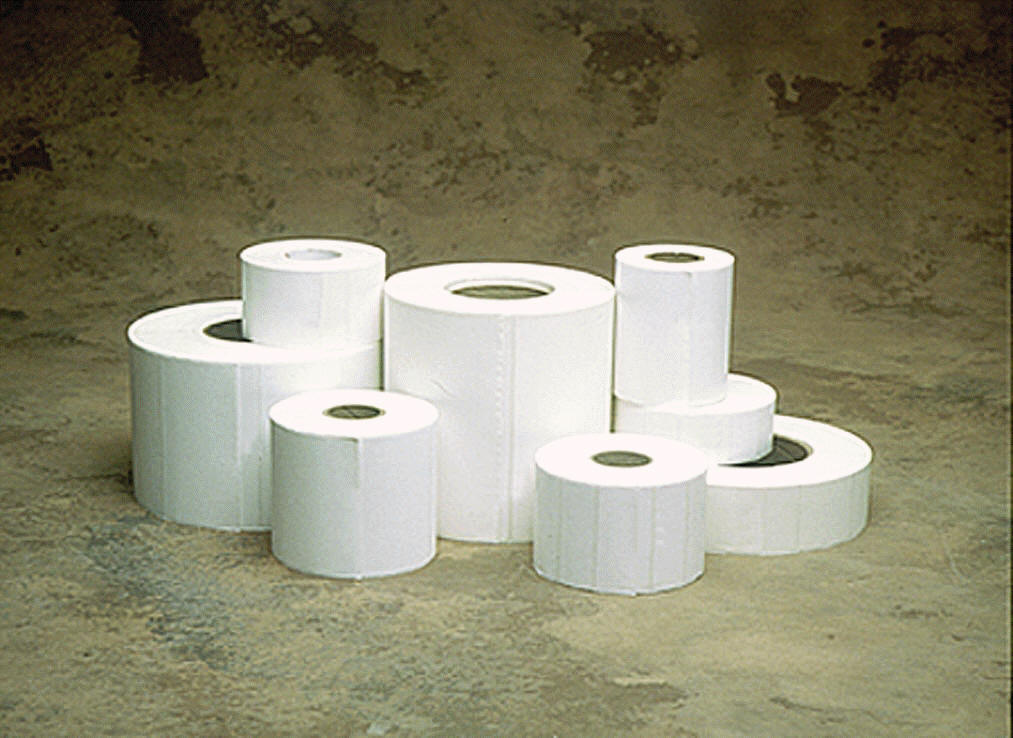
Transfer tape, primarily a tool for vinyl application, isn’t designed for laminating tasks, which typically require materials explicitly meant for surface bonding and protection, like laminating films. While transfer tape aids in precise alignment and bubble reduction for decals, it’s not a substitute for specialized laminating solutions. This brings forth the inquiry of how one might navigate the intricacies of achieving a seamless lamination process using the right tools and techniques.
Understanding Transfer Tape and Its Functionality
While often overlooked, transfer tape plays an essential role in the application of vinyl decals, acting as a temporary adhesive to guarantee precise alignment on various surfaces. This tool’s primary purpose is to hold decals securely, facilitating proper placement on substrates like wood or glass. The benefits of transfer tape extend to its ability to maintain material stability during lamination, allowing for controlled liner removal post-application. Different adhesive types cater to specific needs—StandardGrip works well with permanent and removable vinyl, whereas StrongGrip is better suited for textured materials like glitter vinyl. Proper use of transfer tape mitigates common application issues like wrinkles and bubbles, ensuring high-quality results and demonstrating its irreplaceable role in lamination processes.
Material Compatibility and Considerations
Understanding transfer tape’s role in vinyl decal application sets the stage for examining its compatibility with various materials. Material requirements for transfer tapes involve adhesion to low-surface-energy materials like polyethylene and polypropylene, where standard adhesives may fail. Acrylic-based adhesives, such as 3M™ 200MP, exhibit strong adhesive properties with metals and high-surface-energy plastics. Double-coated tapes offer precise bonding between dissimilar substrates without leaving residue. For specialized applications, formulations like polyurethane or glass cloth tapes manage extreme temperatures up to 395°F. Additionally, low fogging adhesives guarantee compliance with low VOC requirements, essential in automotive interiors. When selecting adhesives, considerations include UV and humidity resistance, shear strength, and repositioning capabilities to meet industry standards across various sectors.
Manual vs. Automated Lamination Techniques
In the domain of lamination, distinguishing between manual and automated techniques reveals critical differences that impact efficiency and precision. Manual lamination offers advantages like hands-on control and adaptability. Utilizing squeegee tools and methods such as the “taco method,” operators achieve even pressure across substrates, minimizing air bubbles. This technique supports intricate tasks, including multi-layer vinyl designs, using alignment marks for registration control. In contrast, automated lamination excels in precision and speed. Machines optimize unwind tension and nip pressure, considerably reducing cross-web tunneling. They enhance bubble reduction by increasing nip temperature, particularly for UV-printed graphics. Furthermore, automated systems accommodate various substrates, ensuring consistent results. Both techniques provide unique benefits, catering to specific lamination needs and project requirements.
Tackling Common Challenges in Lamination
Exploring the intricacies of lamination, it’s clear that both manual and automated techniques present their unique challenges. Key issues arise from material compatibility and adhesive properties. Selecting the correct tape type is vital; for example, StandardGrip tapes suit permanent or removable vinyl, while StrongGrip is necessary for textured varieties. Inaccurate tape adhesion can irrevocably damage vinyl graphics. Uneven squeegee pressure during application often leads to bubble and wrinkle formation, necessitating tools like burnishing scrapers for ideal contact. Tunneling and liner separation are exacerbated by rigid overlaminates and improper winding techniques, emphasizing the need for correct winding practices. Human error, such as insufficient squeegee burnishing or improper registration, further complicates the process, highlighting the importance of precision and technique.
Post-Processing Care and Maintenance
While guaranteeing successful lamination outcomes, focusing on post-processing care and maintenance is essential. Conducting post lamination checks is critical for identifying potential issues like bubbles or edge lifting. Immediate cooling post-application is necessary to prevent adhesive ooze, preserving adhesive longevity. Uniform pressure applied with squeegees or rollers guarantees consistent bond strength, avoiding stress points. Excess pressure should be avoided as it risks trapping air, undermining the adhesion. Edge trimming is recommended to eliminate excess tape that could lead to delamination. Long-term adhesive performance is supported by storing materials in dry, UV-protected environments, preventing degradation. Additionally, controlling humidity is fundamental for avoiding hydrolysis in water-sensitive adhesives, guaranteeing the longevity of the laminated product.
Equipment Requirements and Specifications
Lamination processes require specific equipment to guarantee high-quality adhesive application, particularly in wide web formats. Proper equipment calibration is essential to guarantee consistent pressure application, especially with pressure-sensitive adhesives requiring 1.5-20 PLI during lamination. Adhesive selection plays a fundamental role in determining the equipment specifications needed, such as the use of 3M™ VHB™ Acrylic Foam Tapes for rigid components. Technical specifications, like product master widths ranging from 48″ to 54″ and varying adhesive thicknesses, influence the equipment’s adaptability. The machinery must also accommodate different liner types, such as 55# Densified Kraft and 83# Polycoated Kraft. For inquiries about equipment, potential users can contact sales assistance at 1-800-362-3550, assuring ideal setup and performance.
Application Tips for Optimal Results
To achieve ideal results with transfer tape application, meticulous attention to surface preparation is paramount. Confirming cleanliness and dryness of surfaces is vital for adhesion. Application techniques, such as using burnishing tools and the taco method, enhance precision. For bubble prevention, gradual unrolling of tape is significant, and employing a bubble scraper after application smooths out trapped air. The wet application method with a water-soap mixture aids flat surfaces like glass. Even pressure during transfer and proper alignment via registration stars or the hinge method guarantees wrinkle-free lamination. Post-application, partial peel checks verify placement accuracy, while re-burnishing addresses adhesion issues. Selecting the right transfer tape and maintaining sharp tools further optimize results.
Frequently Asked Questions
Can Transfer Tape Be Used With Heat-Sensitive Materials?
Transfer tape’s heat transfer properties guarantee material compatibility with heat-sensitive materials by activating adhesives at controlled temperatures. It prevents overheating, allowing precise bonding without damaging substrates like PVC, rubber, or delicate composites, maintaining their structural integrity.
What Are the Environmental Impacts of Using Transfer Tape?
Transfer tape poses sustainability concerns due to its non-biodegradable materials and limited recycling options. Plastic polymers persist environmentally, and adhesives complicate recycling. Alternatives like plant-based tapes offer eco-friendly solutions but face cost and durability challenges.
How Can Transfer Tape Affect Color Vibrancy in Printed Graphics?
Transfer tape affects color vibrancy by altering color saturation and ink adhesion. Misalignment or improper adhesive strength can cause layer shifts, leading to reduced vibrancy. Environmental factors further complicate adhesion, impacting the overall color quality.
Is Transfer Tape Reusable for Multiple Lamination Projects?
Transfer tape reusability is limited; its durability decreases with each use. Stickiness deteriorates, especially with complex designs. Dust and moisture further compromise adhesion. Ideally, transfer tape serves two to three projects before losing effectiveness entirely.
What Is the Cost Comparison Between Transfer Tape and Other Lamination Methods?
She conducts a cost analysis, comparing transfer tape with other methods. Transfer tape costs $0.15-$1.66/ft, whereas alternatives like Duck Brand liner cost ~$0.10/ft. Material comparison shows transfer tape is more expensive, influencing lamination choice.