What Is Laminating Tape Used For?
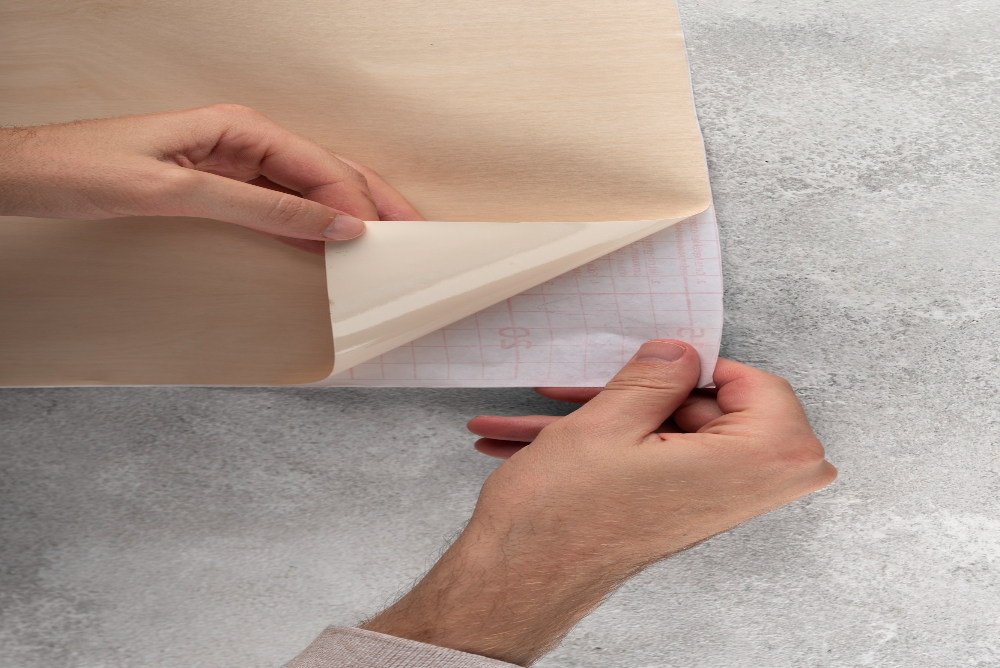
Laminating tape serves an essential role across numerous sectors due to its superior bonding and protective characteristics. In the food industry, it acts as a moisture and contamination barrier, enhancing safety. Pharmaceutical applications benefit from its high barrier properties, critical for safeguarding medications. Electronics packaging utilizes anti-static features to protect sensitive components. Additionally, its resistance to abrasions, chemicals, and UV exposure in industrial contexts underscores its efficiency in reducing operational costs. But what makes it indispensable?
Packaging Applications in the Food Industry
Laminating tape plays an essential role in packaging applications within the food industry, offering a suite of benefits tailored to enhance product protection and compliance. Its multi-layer composition, typically combining polyethylene and polyester, creates a robust barrier against moisture and contamination, essential for food safety. The tape’s ability to maintain structural integrity at low freezer temperatures guarantees packaging efficiency across various environments. FDA compliance for direct food contact underscores its suitability in food applications. Additionally, laminating tape enhances packaging efficiency through its peel-off functionality, facilitating resealable packs without leaving adhesive residue. This feature supports portion control and reduces food waste. By maintaining seal integrity despite temperature fluctuations, it secures food products, preventing bacterial growth and guaranteeing consumer safety.
Pharmaceutical Packaging and Protective Laminating
In the domain of pharmaceutical packaging, the integration of protective laminating materials is essential for ensuring product efficacy and safety. High barrier laminates, including aluminum foil and metallized polyester, shield medications from humidity and contaminants, aligning with pharmaceutical safety protocols. FFS unit dose packaging facilitates precise API dosing, while single-dose oral containers eliminate contamination risks. Laminates composed of PET, PA, or PVC offer mechanical durability, essential under cleanroom standards, and resist puncturing and deformation. They remain intact during sterilization processes like gamma radiation. Multi-layer structures, such as metallized PET/polyamide/PE, provide ultra-barrier protection. Compliance with GB9685 and YBB packaging standards is mandatory, ensuring non-toxic adhesive use and maintaining aroma and flavor integrity in sensitive formulations.
Anti-Static Tapes in Electronics Packaging
Protective laminating materials in pharmaceutical packaging serve as a foundation for safeguarding sensitive products, much like anti-static tapes in electronics packaging protect electronic components. These tapes offer significant anti-static benefits, ensuring electronic safety by sealing anti-static packaging bags to prevent static leakage during transport. By bundling electronic components, they minimize friction-induced static, a critical factor in handling sensitive devices. Anti-static tapes secure components in blister packs with pressure-sensitive adhesive, providing a stable environment for storage and transport. They also play a pivotal role in grounding static charges, creating low-resistance pathways to dissipate harmful electrostatic discharge (ESD). Additionally, anti-static tapes are essential in labeling and isolating static-sensitive devices, facilitating precise application during the assembly process.
Barrier Functions Against Industrial Contaminants
Even as industries face a myriad of environmental challenges, laminating tape excels as a robust barrier against industrial contaminants. In industrial applications, these tapes serve as contaminant barriers by effectively sealing against moisture, dust, and chemical vapors. With advanced moisture protection, they block water vapor and humidity, minimizing degradation risks. UV-resistant layers prevent damage from prolonged exposure to sunlight, while temperature stability guarantees performance in extreme conditions from -40°C to 107°C. Additionally, laminating tapes exhibit solvent resistance, standing up to industrial fluids such as toluene and turpentine, maintaining adhesive cohesion against corrosive liquids. Their abrasion resistance safeguards surfaces from mechanical wear, while cross-linked polymers enhance durability against aggressive chemicals, making them indispensable in industrial settings.
Enhancing Structural Integrity in Automotive and Aerospace
Laminating tape revolutionizes structural integrity in both the automotive and aerospace sectors by offering advanced bonding solutions. In automotive bonding, it effectively joins diverse materials like steel and polycarbonate, creating seamless joints in components such as door panels. This reduces leakage and eliminates the need for heavy mechanical fasteners, thereby decreasing vehicle weight and enhancing performance. By preventing vibration-induced stress fractures, it guarantees durability, especially in engine components.
In aerospace adhesion, laminating tape seals lightweight composites in aircraft panels, maintaining pressure stability and protecting against fluid contamination. It fortifies fuel line joints and manages thermal and mechanical stress, guaranteeing adhesion integrity under fluctuating temperatures and high-vibration environments like propulsion systems. This contributes to overall safety and efficiency in both industries.
Layer-Lamination Techniques and Adhesive Uses
Building on the robust applications of laminating tape in automotive and aerospace sectors, layer-lamination techniques further expand its versatility by offering specialized bonding methods. Extrusion lamination involves bonding materials like PET and aluminum using an extruded LDPE layer, guaranteeing adhesive compatibility and strong layer adhesion. This method requires substrate preparation with primers or hot substrates, enhancing adhesion quality. LDPE’s role in modifying barriers for food packaging highlights its versatility, while EVA is essential for heat-resistant applications, such as healthcare pouches. Modified polyolefins, especially anhydride-modified, enhance adhesion to aluminum surfaces. Solvent-based PUR adhesives, used in dry-bond methods, guarantee robust bonds without curing delays. These techniques maximize efficiency and adaptability across diverse industrial applications.
Multi-Layer Constructions With Various Materials
When exploring multi-layer constructions with various materials, the integration of substrates like films, foams, and plastics elevates product performance by enhancing strength, stiffness, and durability. Custom laminate designs utilize pressure-sensitive adhesives to bond diverse materials such as aluminum foil or fabrics, creating robust, wear-resistant structures. Hybrid material integration allows for the creation of self-adhesive laminates, converting non-adhesive substrates into versatile solutions. High-performance double-sided tapes facilitate the construction of intricate multi-layer designs, accommodating materials sourced from suppliers or customer provisions. Techniques like heat-assisted laminating and island placement guarantee precision in structural alignment. These advanced processes and materials optimize laminate functionality, enabling tailored solutions for complex industrial applications, enhancing both efficiency and material performance in demanding environments.
Environmental Resistance and Durability Features
In the domain of laminating tape applications, environmental resistance and durability play a pivotal role in determining product success, particularly in harsh or variable conditions. Modified acrylic adhesives offer environmental stability by resisting UV degradation and chemicals, ensuring adhesive longevity. Outdoor-grade tapes withstand repetitive sun exposure without degradation, while specialty formulations stick effectively to polar and non-polar substrates. High-shear strength materials prevent detachment under environmental stressors. Temperature stability is achieved through optimized adhesives that handle extreme heat and resist freezing, thereby maintaining bond integrity. Water and moisture protection are guaranteed by solvent-based adhesives forming hydrophobic barriers, and multi-layer structures redirect moisture. Structural integrity is bolstered by continuous lamination, ensuring long-term performance across diverse environments.
Cost-Effective Bonding Solutions in Industrial Settings
A variety of cost-effective bonding solutions in industrial settings leverage laminating tape to maximize efficiency and reduce expenses. Laminating tape facilitates cost reduction through material efficiency by enabling bonding across diverse substrates with a single tape type. This reduces inventory complexity and streamlines supply chains. The tape’s thin yet durable design optimizes material usage, maintaining strength while conserving resources. Adhesive compatibility across plastics, metals, and composites further minimizes the need for multiple bonding agents, enhancing cost-effectiveness. Automated integration with industrial laminators and standard roll sizes reduce material waste and labor costs, while clean finishes eliminate secondary cleaning steps. Additionally, laminating tapes offer low application skill requirements, accelerating worker training and minimizing production delays, collectively enhancing operational efficiency and cost savings.
Frequently Asked Questions
How Does Laminating Tape Compare to Traditional Mechanical Fasteners?
Laminating tape offers strong adhesive bonds with minimal surface preparation compared to traditional mechanical fasteners. While tapes excel in lightweight applications, fasteners provide superior load capacity and durability, especially in environments requiring frequent adjustments or subject to dynamic loads.
Can Laminating Tape Be Used for Decorative Purposes?
Laminating tape enhances decorative applications by adding a protective layer to creative packaging designs. It provides durability, gloss, and stability to materials like paper and fabric, ensuring lasting visual appeal in both personal and professional crafting projects.
What Are the Limitations of Laminating Tape in Extreme Environments?
Laminating tape’s adhesive properties face challenges in extreme environments. Temperature sensitivity affects performance, with high heat causing melting and extreme cold making adhesives brittle. Rapid thermal cycling and UV exposure further compromise durability, risking bond failure and discoloration.
How Is Laminating Tape Disposed of or Recycled?
Laminating tape’s disposal involves lifecycle analysis to assess waste management strategies. Specialized facilities use chemical processes for recycling, while incineration or upcycling options exist. Improper disposal risks environmental harm, so secure methods and creative reuse are recommended.
Are There Specific Industries That Should Avoid Using Laminating Tape?
Industries like electronics, aerospace, and pharmaceuticals should avoid laminating tape due to safety concerns and industry regulations. Its susceptibility to environmental factors and static issues compromise reliability and quality, impacting critical applications and precision manufacturing processes.