- Home
- /
- Lamination Tape
Lamination Tape
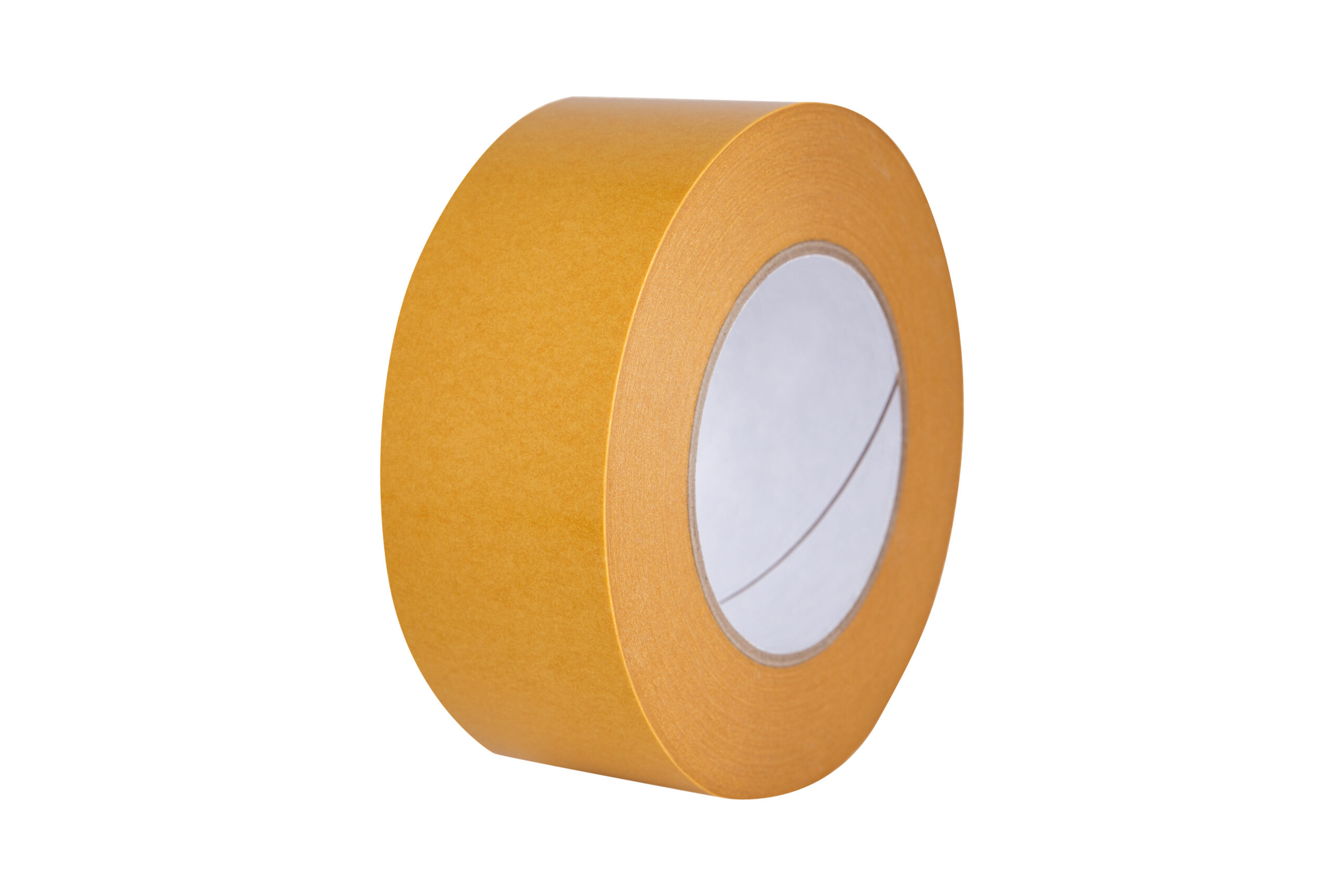
VIEW SPECSHEET
Y2070
Carrier: None (Unsupported transfer tape)
Adhesive: Solvent-based acrylic adhesive offering strong initial tack and excellent adhesion to a wide variety of substrates. It provides long-term bonding, ensuring reliable performance in demanding environments.
Thickness: 4 mils (0.10 mm)
Color: Clear
Liner: Paper liner with excellent release properties, designed to facilitate easy handling and application.
Liner Color: Mustard
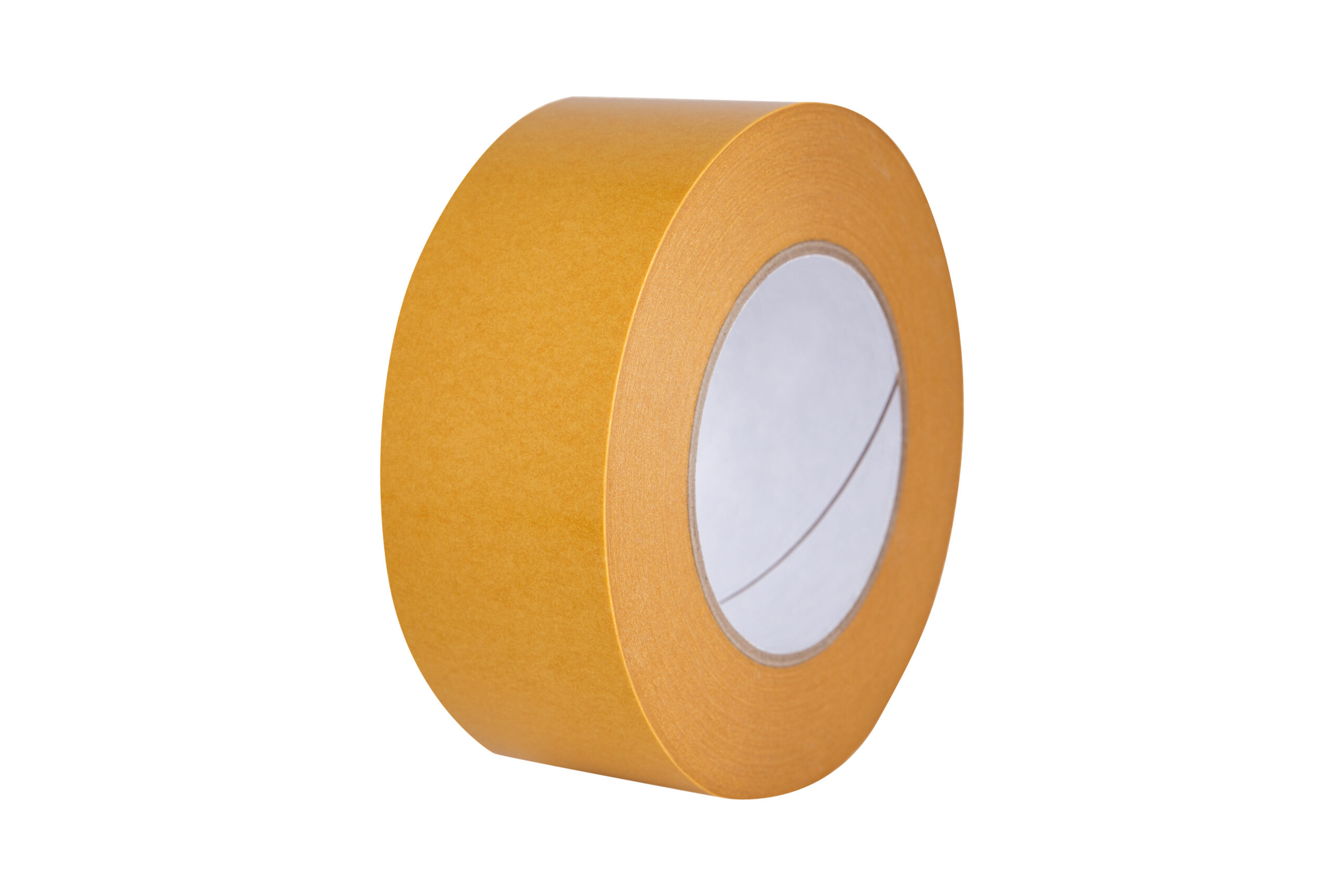
VIEW SPECSHEET
Y207H
Carrier: None (Unsupported transfer tape)
Adhesive: Acrylic solvent-based adhesive offering exceptional adhesive performance and good temperature and chemical resistance. The thick coating weight provides excellent laminating results on low energy surfaces, even under extreme environmental conditions.
Thickness: 4 mils (0.10 mm)
Color: Clear
Liner: Paper liner with excellent release properties, designed to facilitate easy handling and application.
Liner Color: Mustard
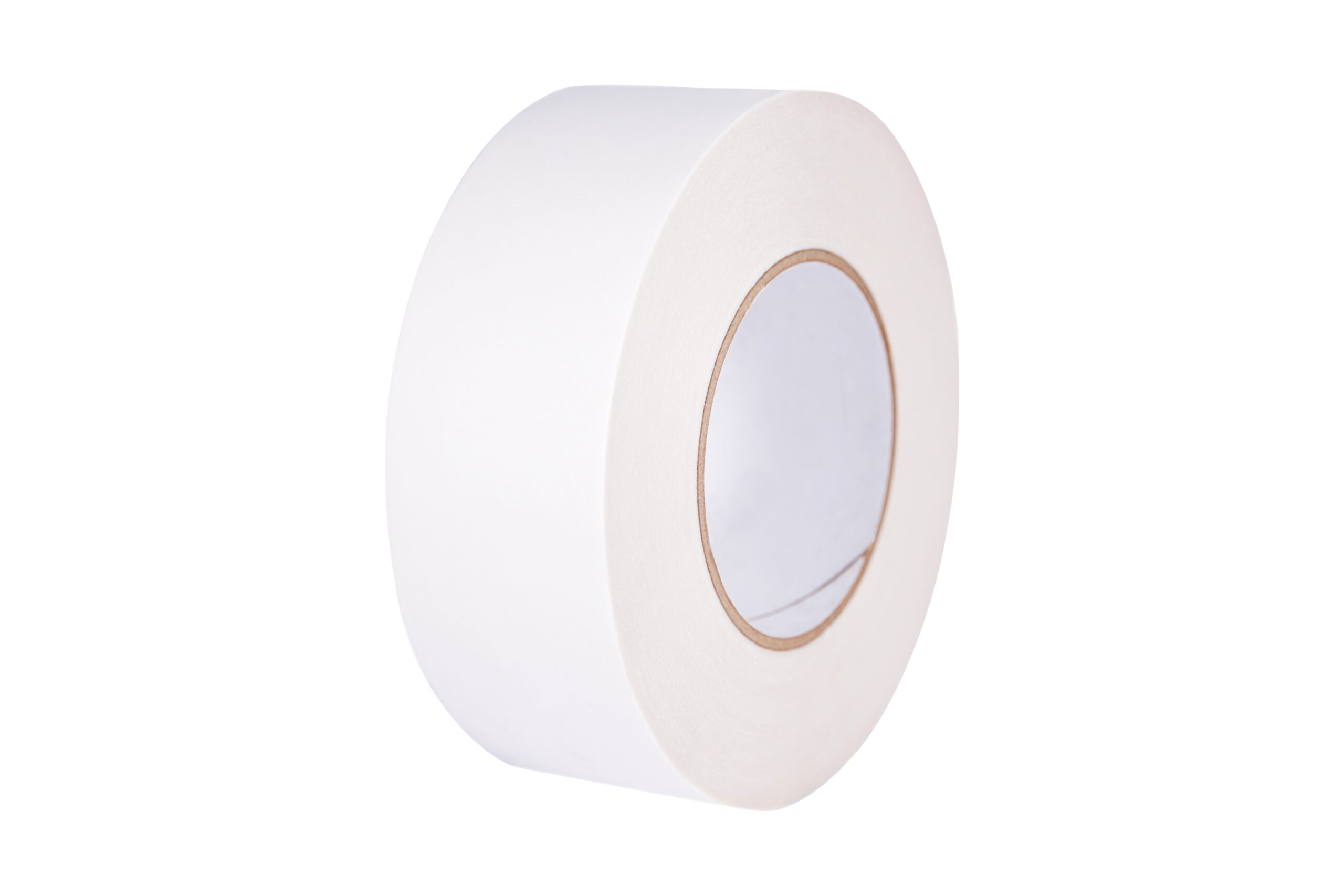
VIEW SPECSHEET
W2010
Carrier: Transfer
Adhesive: Acrylic solvent-based adhesive offering exceptional adhesive performance and resistance to extreme temperatures, chemicals, and water. The adhesive formulation enables secure bonding to low-surface energy surfaces in demanding environmental conditions and provides excellent laminating results.
Thickness: 4 mils (0.10 mm)
Color: Clear
Liner: Paper liner with excellent release properties, designed to facilitate easy handling and application.
Liner Color: White
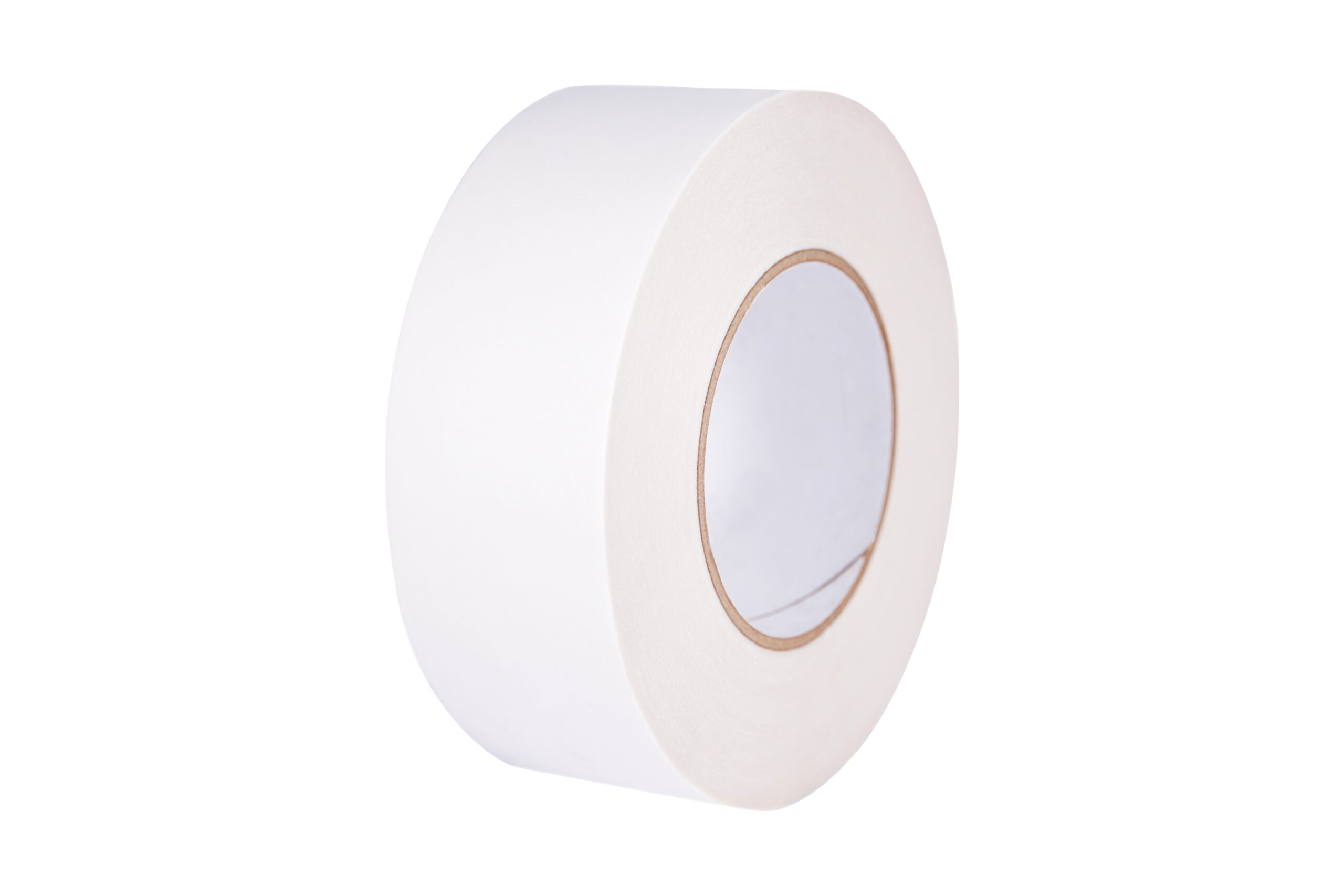
VIEW SPECSHEET
W2060
Carrier: Transfer
Adhesive: Acrylic solvent-based adhesive offering exceptional adhesive performance and resistance to extreme temperatures, chemicals, and water. The adhesive formulation enables secure bonding to low-surface energy surfaces in demanding environmental conditions and provides excellent laminating results.
Thickness: 2.4 mil ± 0.2 mil
Color: Clear
Liner: Paper liner with excellent release properties, designed to facilitate easy handling and application.
Liner Color: White
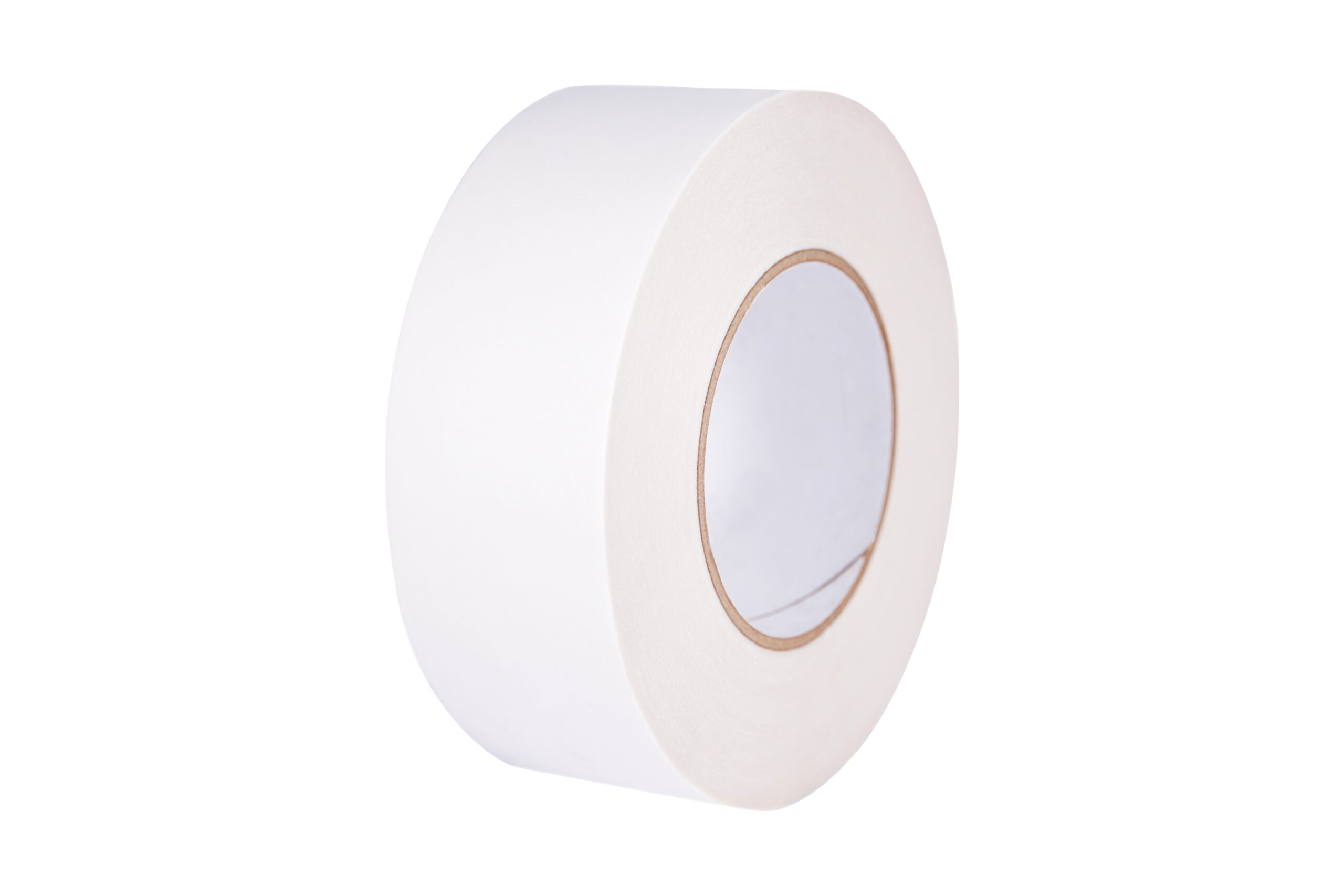
VIEW SPECSHEET
H2050
Carrier: Transfer
Adhesive: Acrylic solvent-based adhesive offering exceptional adhesive performance and resistance to extreme temperatures, chemicals, and water. The adhesive formulation enables secure bonding to low-surface energy surfaces in demanding environmental conditions and provides excellent laminating results.
Thickness: 2.0 mils (0.05 ± 0.002 mm)
Color: Clear
Liner: Paper liner with excellent release properties, designed to facilitate easy handling and application.
Liner Color: White
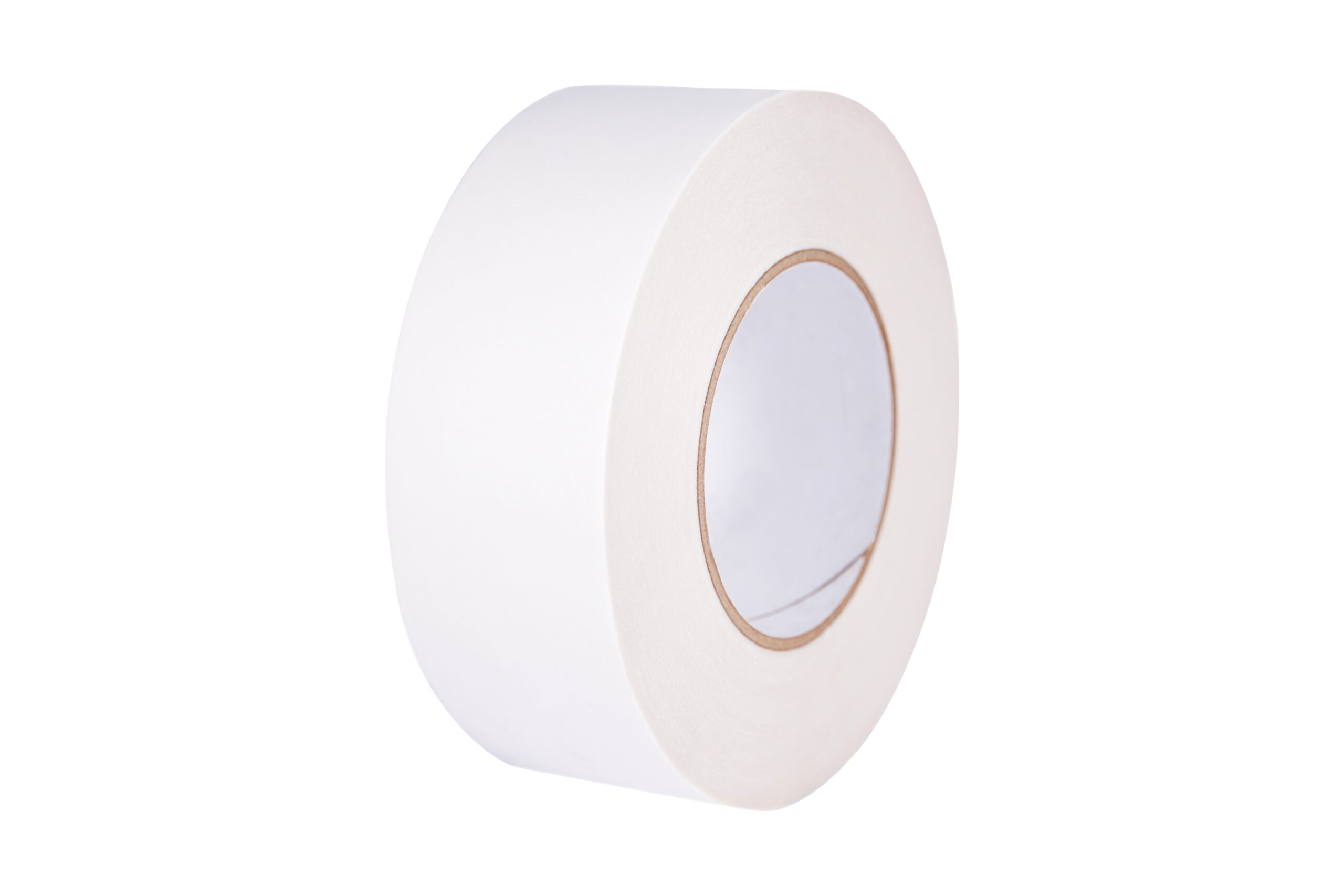
VIEW SPECSHEET
S2050
Carrier: Transfer
Adhesive: Modified acrylic solvent-based adhesive offering outstanding performance, including chemical and UV resistance, providing long-term bonding strength. Exhibits superior temperature resistance and high shear strength, effectively resisting edge picking and part slippage. Demonstrates excellent adhesion to most low surface energy surfaces.
Thickness: 2 mils ± 0.2 mil
Color: Clear
Liner: Paper liner with excellent release properties, designed to facilitate easy handling and application.
Liner Color: White
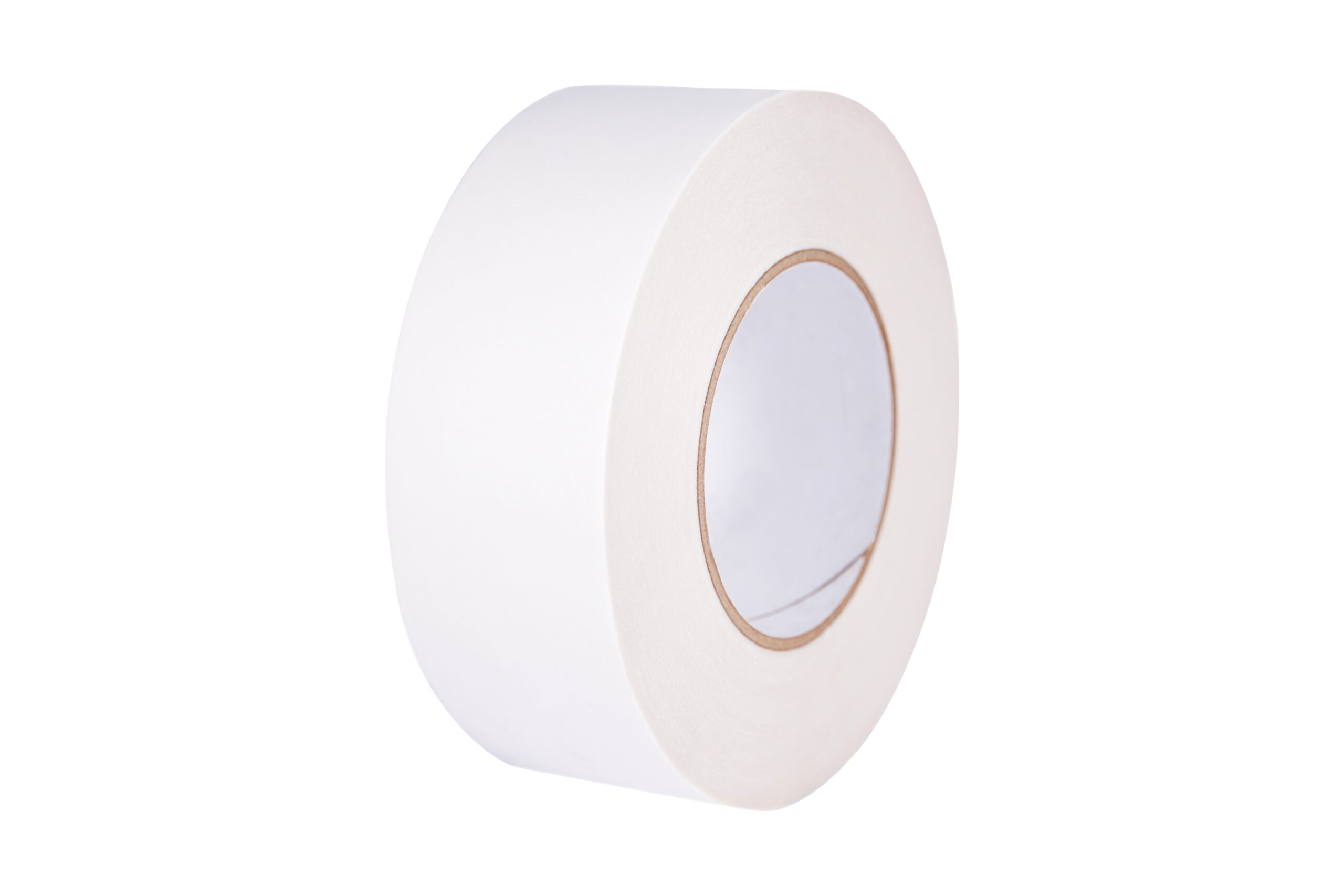
VIEW SPECSHEET
W2970
Carrier: Film
Adhesive: Acrylic solvent-based adhesive offering high adhesion levels, providing quick bonding results. Ideal for a wide variety of substrates where a high adhesion level is required.
Thickness: 5 mil
Color: Clear
Liner: Paper liner with excellent release properties, designed to facilitate easy handling and application.
Liner Color: White
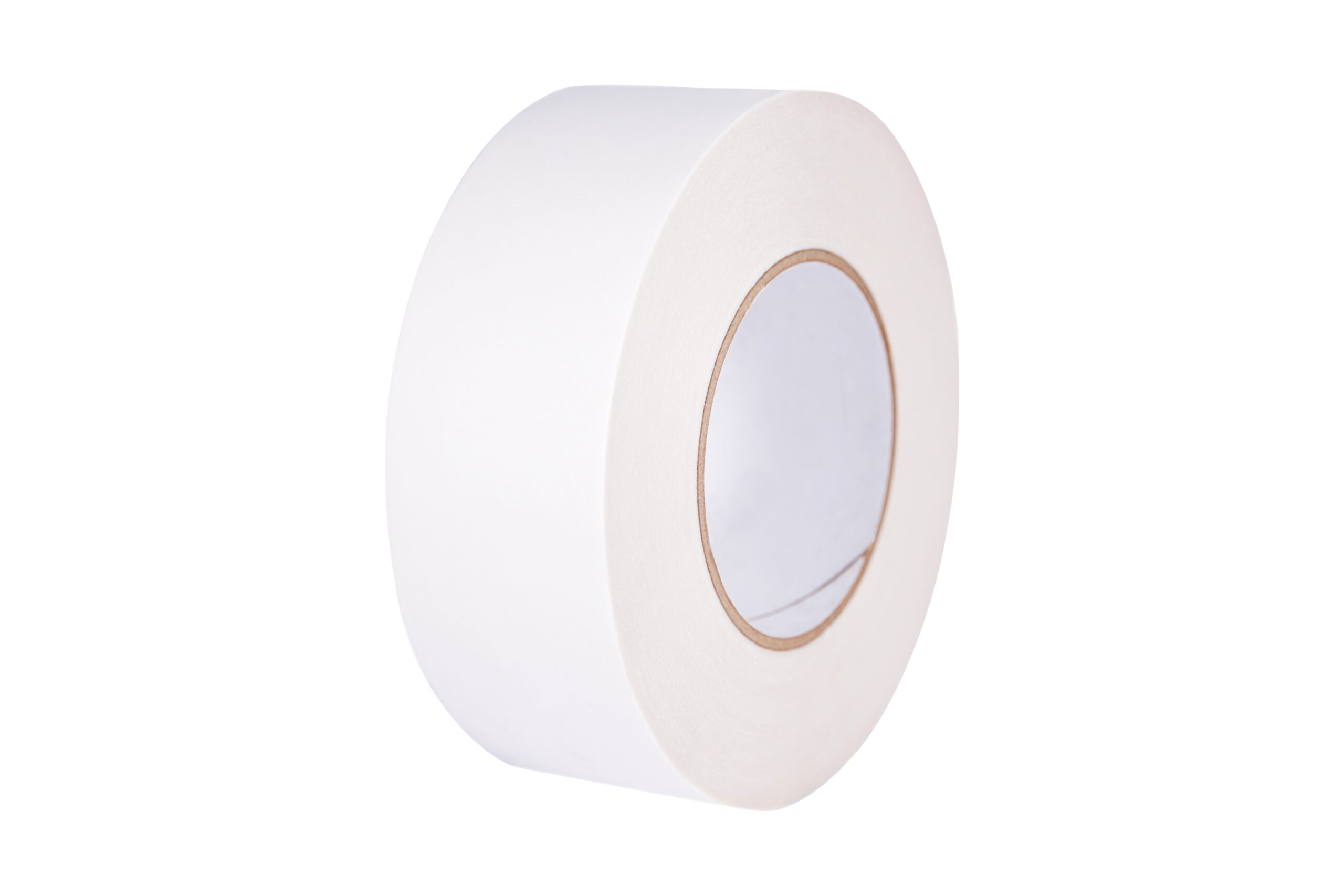
VIEW SPECSHEET
H2470
Carrier: Tissue
Adhesive: Acrylic solvent-based adhesive featuring a high grab tack adhesive system, providing quick bonding results even on most low surface energy substrates. Highly recommended for splicing, bonding, and laminating porous objects.
Thickness: 4.7 mil (0.12 ± 0.01 mm)
Color: Clear
Liner: Paper liner with excellent release properties, designed to facilitate easy handling and application.
Liner Color: White
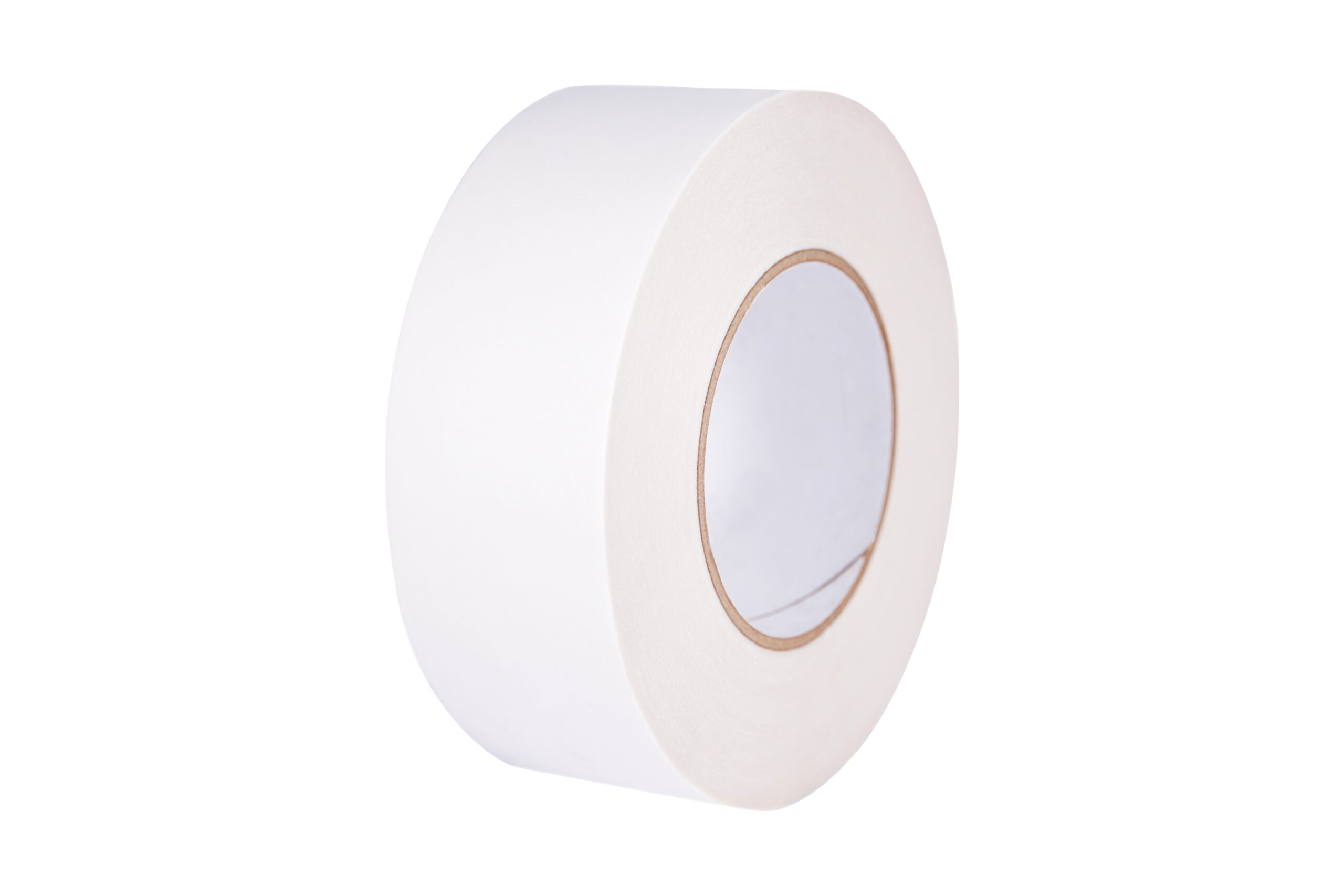
VIEW SPECSHEET
F2480
Carrier: Tissue
Adhesive: Acrylic solvent-based adhesive offering a high grab adhesive system, providing quick laminating results across a wide temperature range. Exhibits chemical and UV resistance.
Thickness: 3.1 mil
Color: White
Liner: Paper liner with excellent release properties, designed to facilitate easy handling and application.
Liner Color: White
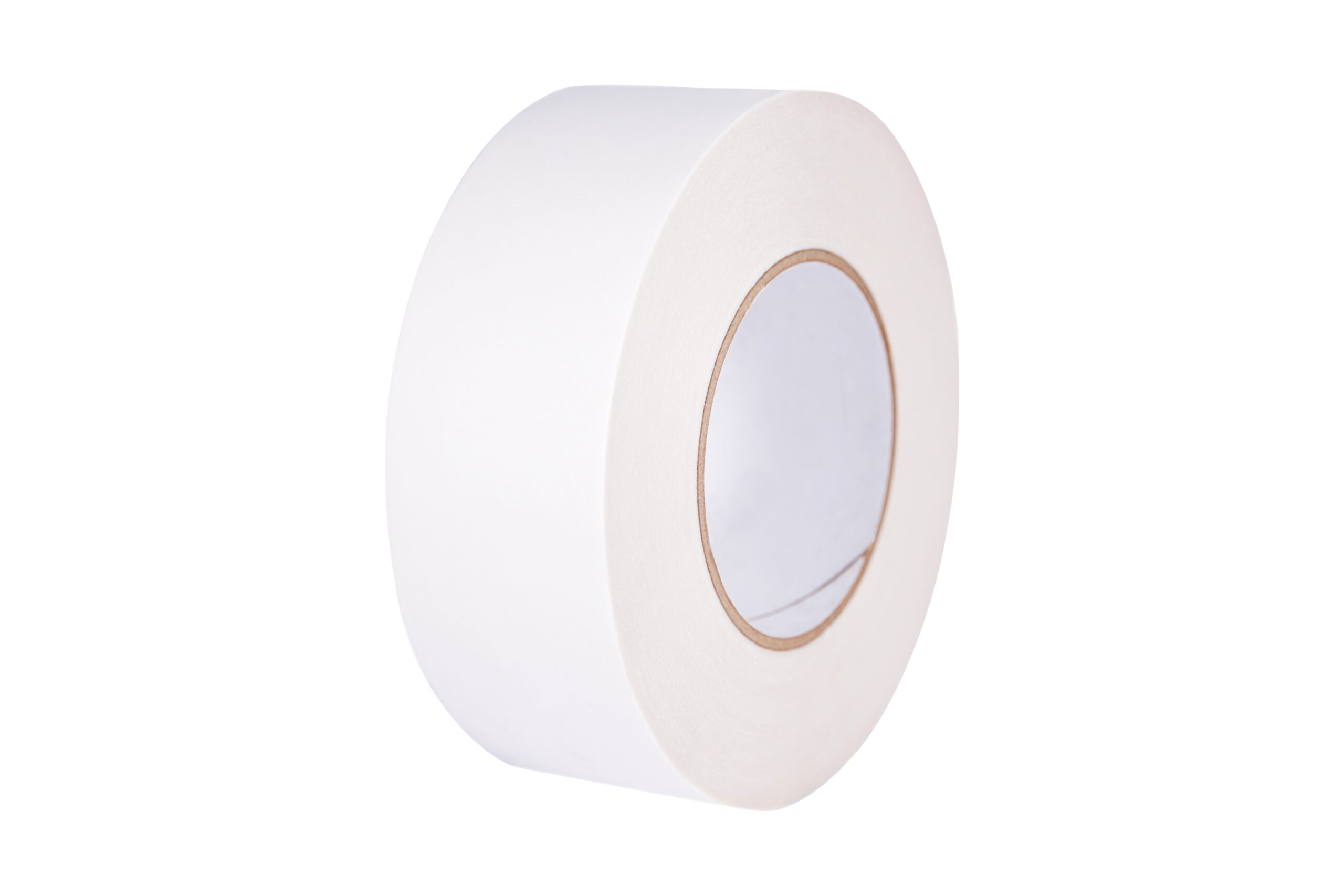
VIEW SPECSHEET
H248B
Carrier: Tissue
Adhesive: Acrylic solvent-based adhesive featuring a high grab tack adhesive system, providing quick bonding results even on most low surface energy substrates. Highly recommended for splicing, bonding, and laminating porous objects.
Thickness: 5 mil (0.13 ± 0.01 mm)
Color: White
Liner: Paper liner with excellent release properties, designed to facilitate easy handling and application.
Liner Color: White
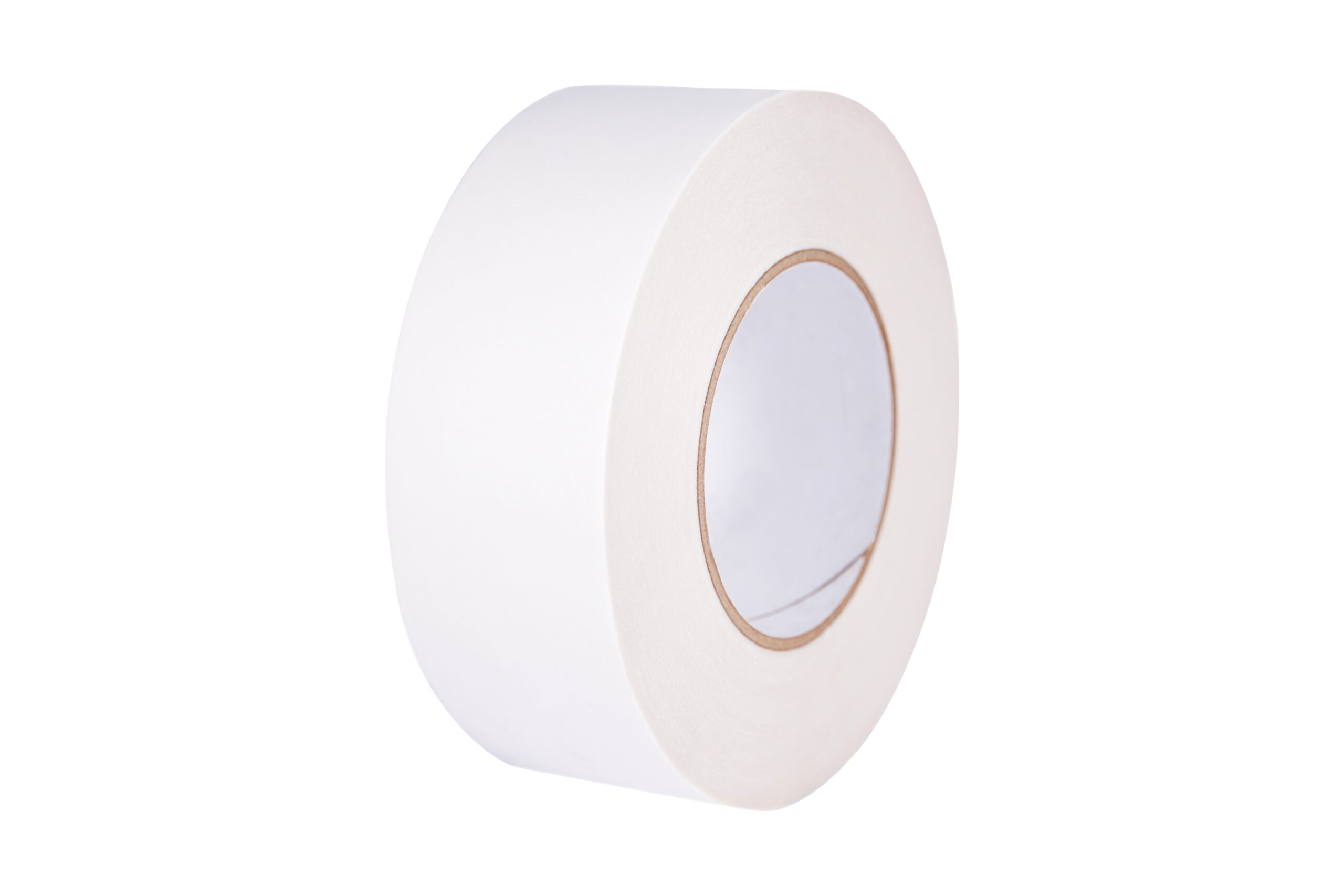
VIEW SPECSHEET
H2970
Carrier: 1/2 mil PET film
Adhesive: Solvent acrylic adhesive offering high grab tack and quick bonding results, even on most low surface energy substrates. Highly recommended for splicing, bonding, and laminating porous objects. Offers good resistance to solvents, heat, and chemicals.
Thickness: 4.3 mil (0.11 ± 0.01 mm)
Color: Clear
Liner: Polycoated bleached Kraft paper with excellent release properties, designed to facilitate easy handling and application.
Liner Color: White
What Is Lamination Tape?
Pressure sensitive lamination tape is a type of adhesive tape that forms a strong bond with a surface simply through the application of pressure—no heat, water, or solvent activation is required. It typically consists of a carrier material (such as film or tissue) coated with a pressure sensitive adhesive (PSA) on one or both sides. These tapes are widely used in lamination processes to bond layers of materials together, offering a quick, clean, and efficient alternative to liquid adhesives. Pressure sensitive lamination tapes are valued for their ease of use, consistent adhesive thickness, and ability to bond to a variety of substrates, making them ideal for applications in signage, graphics, electronics, and industrial assembly.
Diverse Applications Across Industries For Lamination Tape
Lamination tape is an effective solution for bonding dissimilar materials together, providing strong and reliable adhesion between substrates with varying surface properties.
- Metal to Plastic:
- Example: Bonding aluminum (high surface energy) to polypropylene (low surface energy) in electronics, automotive, and consumer goods.
- Application: In automotive manufacturing, PSA lamination tape can be used to attach metal panels to plastic body parts without the need for rivets or welding. It’s also used in electronics for assembling components where metal and plastic parts need to be securely held together, such as in smartphones or laptops, offering durability and resistance to vibrations or impacts.
- Benefit: The tape provides immediate adhesion, and unlike liquid adhesives or heat bonding, it doesn’t require curing time, making assembly processes faster and more efficient.
- Fabric to Plastic:
- Example: Bonding nylon nonwoven fabrics (used for upholstery, insulation, or filters) to ABS plastic in automotive interiors and appliance manufacturing.
- Application: In the automotive sector, PSA lamination tape is frequently used to bond fabric-based materials like seat covers or headliners to hard plastic panels, providing a quick and clean solution for assembling interior components. Similarly, in appliances, it can bond fabrics (such as felt for filters) to plastic components in washing machines or dishwashers.
- Benefit: The tape adheres immediately, without the need for drying or curing times, allowing manufacturers to quickly move from one production step to another. It also reduces the risk of fabric distortion, which can happen with heat-based bonding methods.
- Foam to Metal:
- Example: Bonding polyurethane foam to smooth metal surfaces (e.g., in insulation applications in HVAC systems or automotive soundproofing).
- Application: In automotive soundproofing, PSA lamination tape can bond sound-damping foam to metal surfaces in doors, floors, or the cabin ceiling. It’s also used in HVAC systems to attach foam seals to metal ducts for insulation purposes. These tapes ensure that foam adheres well to the smooth metal surface, providing effective insulation and soundproofing.
- Benefit: Unlike traditional adhesive methods, PSA lamination tape doesn’t require time to dry or cure, offering an immediate bond that’s critical for mass production environments. The foam also remains firmly in place without the risk of peeling or separation over time.
General Advantages of PSA Lamination Tape:
- Easy to Apply: No special tools, heating, or chemical activation is required. Simply press the tape onto the surface to form a bond.
- Forms a Quick Bond: Instant adhesion allows manufacturers to move swiftly through production lines, saving time and increasing efficiency.
- No Dwell Time Needed: Can be used right away, eliminating the need for waiting times often associated with liquid adhesives or heat-curing processes.
Optimizing Adhesion and Breathability: The Power of Zone-Coated PSA Lamination Tape
Zoning the coating of PSA lamination tape is a technique where adhesive is applied only to specific areas of the carrier material, leaving other sections free of adhesive. This approach is particularly useful in applications where breathability is critical, such as when laminating filtration materials. In such cases, full coverage of adhesive would block airflow, compromising the material’s filtering function. By using a zone-coated PSA tape, manufacturers can apply adhesive in strategic areas to ensure a strong bond, while leaving certain regions without adhesive to maintain the material’s permeability. This creates a breathable stack-up that provides the necessary structural integrity and adhesion, while still allowing the material to perform its intended function, such as filtering air or fluids. Zone coating is ideal for applications in industries like automotive filtration, HVAC systems, or medical products where both bonding strength and breathability are essential.
Choosing the Right Liner for Your Lamination Tape
Each liner type has its specific strengths and limitations, and the best choice depends on the application’s requirements, including cost considerations, environmental exposure, and production efficiency.
Here’s a breakdown of the different types of liners used for lamination tapes, along with their pros and cons:
- PET or PP Film Liner
- Pros:
- Clean Die-Cutting: PET (Polyethylene Terephthalate) or PP (Polypropylene) film liners produce very little or no paper dust when die-cut, resulting in cleaner cuts, especially in applications that require precision.
- Waterproof: These film liners are resistant to moisture, ensuring the liner does not split or degrade, which is particularly beneficial in electronic applications where moisture can cause issues.
- Durability: The film liner is tougher than paper liners and is less likely to tear or break during the production process, providing consistent, uninterrupted production.
- Clean Removal: The film liner allows for easy and clean removal, reducing the risk of contamination or adhesive issues when the tape is applied.
- Cons:
- Cost: PET or PP film liners are generally more expensive than paper liners, making them less cost-effective for high-volume applications where the cost per unit is critical.
- Paper Liner
- Pros:
- Cost-Effective: Paper liners are typically less expensive than film liners, making them ideal for budget-conscious projects or large-scale applications where the cost per unit is a concern.
- eco-friendly: As a more eco-friendly option, paper liners are biodegradable and may be preferred for environmentally conscious applications.
- Good for Standard Applications: Paper liners are effective in general-purpose lamination tapes where moisture resistance and high durability are not as critical.
- Cons:
- Paper Dust: When die-cut, paper liners tend to generate dust, which can lead to contamination issues, especially in cleanroom or high-precision applications.
- Moisture Sensitivity: Paper liners can absorb moisture, causing them to degrade, tear, or split, which can be problematic in certain applications, especially those involving electronics or outdoor use.
- Tear Risk: During production or storage, paper liners can be more prone to tearing, which may cause production delays or inconsistencies in tape application.
Choosing the right liner for your lamination tape is crucial to ensuring optimal performance in your application. At Cactus tape, we understand that every project has unique requirements, whether it’s precision die-cutting, moisture resistance, or environmental considerations. Our team of experts is ready to help you select the ideal liner based on factors such as production speed, adhesive strength, and end-use environment. Whether you need the durability and cleanliness of a PET or PP film liner for electronic applications, or the cost-effectiveness and eco-friendliness of a paper liner for general use, we provide personalized guidance to ensure your tape performs at its best. Contact us today to discuss your specific needs, and we’ll assist you in selecting the most suitable liner to optimize your production process.